Hazardous Waste Operations and Emergency Response
Home More Training Resources OSHA General Industry Training Requirements Hazardous Waste Operations and Emergency Response
OSHA Training Requirements - HAZWOPER
This website is not the official or final authority to determine OSHA compliance responsibilities, which are set forth in OSHA standards themselves, and the Occupational Safety and Health Act of 1970. Because OSHA regulations are constantly being added, deleted, and/or revised, you must not rely on this website as the official or final authority of OSHA training requirements; refer to the official OSHA regulations available on OSHA’s website (osha.gov). – See disclaimers.
1910.120 – Hazardous Waste Operations and Emergency Response
(c)(8) – Employee notification. Any information concerning the chemical, physical, and toxicologic properties of each substance known or expected to be present on site that is available to the employer and relevant to the duties an employee is expected to perform shall be made available to the affected employees prior to the commencement of their work activities. The employer may utilize information developed for the hazard communication standard for this purpose.
(e) – Training.
(1) – General – Hazardous Waste Operations and Emergency Response
(i) All employees working on site (such as but not limited to equipment operators, general laborers and others) exposed to hazardous substances, health hazards, or safety hazards and their supervisors and management responsible for the site shall receive training meeting the requirements of this paragraph before they are permitted to engage in hazardous waste operations that could expose them to hazardous substances, safety, or health hazards, and they shall receive review training as specified in this paragraph.
(ii) Employees shall not be permitted to participate in or supervise field activities until they have been trained to a level required by their job function and responsibility.
(2)- Elements to be covered. The training shall thoroughly cover the following:
(i) Names of personnel and alternates responsible for site safety and health;
(ii) Safety, health and other hazards present on the site;
(iii) Use of personal protective equipment;
(iv) Work practices by which the employee can minimize risks from hazards;
(v) Safe use of engineering controls and equipment on the site;
(vi) Medical surveillance requirements including recognition of symptoms and signs which might indicate over exposure to hazards; and
(vii) The contents of paragraphs (G) through (J) of the site safety and health plan set forth in paragraph (b)(4)(ii) of this section.
(3) – Initial training.
(i) General site workers (such as equipment operators, general laborers and supervisory personnel) engaged in hazardous substance removal or other activities which expose or potentially expose workers to hazardous substances and health hazards shall receive a minimum of 40 hours of instruction off the site, and a minimum of three days actual field experience under the direct supervision of a trained experienced supervisor.
(ii) Workers on site only occasionally for a specific limited task (such as, but not limited to, ground water monitoring, land surveying, or geophysical surveying) and who are unlikely to be exposed over permissible exposure limits and published exposure limits shall receive a minimum of 24 hours of instruction off the site, and the minimum of one day actual field experience under the direct supervision of a trained, experienced supervisor.
(iii) Workers regularly on site who work in areas which have been monitored and fully characterized indicating that exposures are under permissible exposure limits and published exposure limits where respirators are not necessary, and the characterization indicates that there are no health hazards or the possibility of an emergency developing, shall receive a minimum of 24 hours of instruction off the site, and the minimum of one day actual field experience under the direct supervision of a trained, experienced supervisor.
(iv) Workers with 24 hours of training who are covered by paragraphs (e)(3)(ii) and (e)(3)(iii) of this section, and who become general site workers or who are required to wear respirators, shall have the additional 16 hours and two days of training necessary to total the training specified in paragraph (e)(3)(i).
(4) – Management and supervisor training. On-site management and supervisors directly responsible for, or who supervise employees engaged in, hazardous waste operations shall receive 40 hours initial training, and three days of supervised field experience (the training may be reduced to 24 hours and one day if the only area of their responsibility is employees covered by paragraphs (e)(3)(ii) and (e)(3)(iii)) and at least eight additional hours of specialized training at the time of job assignment on such topics as, but not limited to, the employer’s safety and health program and the associated employee training program, personal protective equipment program, spill containment program, and health hazard monitoring procedure and techniques.
(5) – Qualifications for trainers. Trainers shall be qualified to instruct employees about the subject matter that is being presented in training. Such trainers shall have satisfactorily completed a training program for teaching the subjects they are expected to teach, or they shall have the academic credentials and instructional experience necessary for teaching the subjects. Instructors shall demonstrate competent instructional skills and knowledge of the applicable subject matter.
(6) – Training certification. Employees and supervisors that have received and successfully completed the training and field experience specified in paragraphs (e)(1) through (e)(4) of this section shall be certified by their instructor or the head instructor and trained supervisor as having completed the necessary training. A written certificate shall be given to each person so certified. Any person who has not been so certified or who does not meet the requirements of paragraph (e)(9) of this section shall be prohibited from engaging in hazardous waste operations.
(7) – Emergency response. Employees who are engaged in responding to hazardous emergency situations at hazardous waste clean-up sites that may expose them to hazardous substances shall be trained in how to respond to such expected emergencies.
(8) – Refresher training. Employees specified in paragraph (e)(1) of this section, and managers and supervisors specified in paragraph (e)(4) of this section, shall receive eight hours of refresher training annually on the items specified in paragraph (e)(2) and/or (e)(4) of this section, any critique of incidents that have occurred in the past year that can serve as training examples of related work, and other relevant topics.
9) – Equivalent training. Employers who can show by documentation or certification that an employee’s work experience and/or training has resulted in training equivalent to that training required in paragraphs (e)(1) through (e)(4) of this section shall not be required to provide the initial training requirements of those paragraphs to such employees and shall provide a copy of the certification or documentation to the employee upon request. However, certified employees or employees with equivalent training new to a site shall receive appropriate, site specific training before site entry and have appropriate supervised field experience at the new site. Equivalent training includes any academic training or the training that existing employees might have already received from actual hazardous waste site experience.
1910.120 – Appendix C. Compliance guidelines.
2. Training. The training programs for employees subject to the requirements of paragraph (e) of this standard should address: the safety and health hazards employees should expect to find on hazardous waste clean-up sites; what control measures or techniques are effective for those hazards; what monitoring procedures are effective in characterizing exposure levels; what makes an effective employer’s safety and health program; what a site safety and health plan should include; hands on training with personal protective equipment and clothing they may be expected to use; the contents of the OSHA standard relevant to the employee’s duties and function; and employee’s responsibilities under OSHA and other regulations. Supervisors will need training in their responsibilities under the safety and health program and its subject areas such as the spill containment program, the personal protective equipment program, the medical surveillance program, the emergency response plan and other areas.
The training programs for employees subject to the requirements of paragraph (p) of this standard should address: the employer’s safety and health program elements impacting employees; the hazard communication program; the hazards and the controls for such hazards that employees need to know for their job duties and functions. All require annual refresher training.
The training programs for employees covered by the requirements of paragraph (q) of this standard should address those competencies required for the various levels of response such as: the hazards associated with hazardous substances; hazard identification and awareness; notification of appropriate persons; the need for and use of personal protective equipment including respirators; the decontamination procedures to be used; preplanning activities for hazardous substance incidents including the emergency response plan; company standard operating procedures for hazardous substance emergency responses; the use of the incident command system and other subjects. Hands-on training should be stressed whenever possible. Critiques done after an incident which include an evaluation of what worked and what did not and how could the incident be better handled the next time may be counted as training time.
For hazardous materials specialists (usually members of hazardous materials teams), the training should address the care, use and/or testing of chemical protective clothing including totally encapsulating suits, the medical surveillance program, the standard operating procedures for the hazardous materials team including the use of plugging and patching equipment and other subject areas.
Officers and leaders who may be expected to be in charge at an incident should be fully knowledgeable of their company’s incident command system. They should know where and how to obtain additional assistance and be familiar with the local district’s emergency response plan and the state emergency response plan.
Specialist employees such as technical experts, medical experts or environmental experts that work with hazardous materials in their regular jobs, who may be sent to the incident scene by the shipper, manufacturer or governmental agency to advise and assist the person in charge of the incident should have training on an annual basis. Their training should include the care and use of personal protective equipment including respirators; knowledge of the incident command system and how they are to relate to it; and those areas needed to keep them current in their respective field as it relates to safety and health involving specific hazardous substances.
Those skilled support personnel, such as employees who work for public works departments or equipment operators who operate bulldozers, sand trucks, backhoes, etc., who may be called to the incident scene to provide emergency support assistance, should have at least a safety and health briefing before entering the area of potential or actual exposure. These skilled support personnel, who have not been a part of the emergency response plan and do not meet the training requirements, should be made aware of the hazards they face and should be provided all necessary protective clothing and equipment required for their tasks.
There are two National Fire Protection Association standards. NFPA 472 – “Standard for Professional Competence of Responders to Hazardous Material Incidents” and NFPA 471 – “Recommended Practice for Responding to Hazardous Material Incidents”, which are excellent resource documents to aid fire departments and other emergency response organizations in developing their training program materials. NFPA 472 provides guidance on the skills and knowledge needed for first responder awareness level, first responder operations level, hazmat technicians, and hazmat specialist. It also offers guidance for the officer corp who will be in charge of hazardous substance incidents.
(o) – New technology programs.
(1) – The employer shall develop and implement procedures for the introduction of effective new technologies and equipment developed for the improved protection of employees working with hazardous waste clean-up operations, and the same shall be implemented as part of the site safety and health program to assure that employee protection is being maintained.
(p)(7) – Training program – TSD facilities
(i) New employees. The employer shall develop and implement a training program which is part of the employer’s safety and health program, for employees exposed to health hazards or hazardous substances at TSD operations to enable the employees to perform their assigned duties and functions in a safe and healthful manner so as not to endanger themselves or other employees. The initial training shall be for 24 hours and refresher training shall be for eight hours annually. Employees who have received the initial training required by this paragraph shall be given a written certificate attesting that they have successfully completed the necessary training.
(ii) Current employees. Employers who can show by an employee’s previous work experience and/or training that the employee has had training equivalent to the initial training required by this paragraph, shall be considered as meeting the initial training requirements of this paragraph as to that employee. Equivalent training includes the training that existing employees might have already received from actual site work experience. Current employees shall receive eight hours of refresher training annually.
(iii) Trainers. Trainers who teach initial training shall have satisfactorily completed a training course for teaching the subjects they are expected to teach or they shall have the academic credentials and instruction experience necessary to demonstrate a good command of the subject matter of the courses and competent instructional skills.
(p)(8)(iii) – Training – Emergency responders
(A) Training for emergency response employees shall be completed before they are called upon to perform in real emergencies. Such training shall include the elements of the emergency response plan, standard operating procedures the employer has established for the job, the personal protective equipment to be worn and procedures for handling emergency incidents.
Exception #1: an employer need not train all employees to the degree specified if the employer divides the work force in a manner such that a sufficient number of employees who have responsibility to control emergencies have the training specified, and all other employees, who may first respond to an emergency incident, have sufficient awareness training to recognize that an emergency response situation exists and that they are instructed in that case to summon the fully trained employees and not attempt control activities for which they are not trained.
Exception #2: An employer need not train all employees to the degree specified if arrangements have been made in advance for an outside fully-trained emergency response team to respond in a reasonable period and all employees, who may come to the incident first, have sufficient awareness training to recognize that an emergency response situation exists and they have been instructed to call the designated outside fully-trained emergency response team for assistance.
(B) Employee members of TSD facility emergency response organizations shall be trained to a level of competence in the recognition of health and safety hazards to protect themselves and other employees. This would include training in the methods used to minimize the risk from safety and health hazards; in the safe use of control equipment; in the selection and use of appropriate personal protective equipment; in the safe operating procedures to be used at the incident scene; in the techniques of coordination with other employees to minimize risks; in the appropriate response to over exposure from health hazards or injury to themselves and other employees; and in the recognition of subsequent symptoms which may result from over exposures.
(C) The employer shall certify that each covered employee has attended and successfully completed the training required in paragraph (p)(8)(iii) of this section, or shall certify the employee’s competency for certification of training shall be recorded and maintained by the employer.
(q)(6) – Training. Training shall be based on the duties and function to be performed by each responder of an emergency response organization. The skill and knowledge levels required for all new responders, those hired after the effective date of this standard, shall be conveyed to them through training before they are permitted to take part in actual emergency operations on an incident. Employees who participate, or are expected to participate, in emergency response, shall be given training in accordance with the following paragraphs:
(i) First responder awareness level. First responders at the awareness level are individuals who are likely to witness or discover a hazardous substance release and who have been trained to initiate an emergency response sequence by notifying the proper authorities of the release. They would take no further action beyond notifying the authorities of the release. First responders at the awareness level shall have sufficient training or have had sufficient experience to objectively demonstrate competency in the following areas:
(A) An understanding of what hazardous substances are, and the risks associated with them in an incident.
(B) An understanding of the potential outcomes associated with an emergency created when hazardous substances are present.
(C) The ability to recognize the presence of hazardous substances in an emergency.
(D) The ability to identify the hazardous substances, if possible.
(E) An understanding of the role of the first responder awareness individual in the employer’s emergency response plan including site security and control and the U.S. Department of Transportation’s Emergency Response Guidebook.
(F) The ability to realize the need for additional resources, and to make appropriate notifications to the communication center.
(ii) First responder operations level. First responders at the operations level are individuals who respond to releases or potential releases of hazardous substances as part of the initial response to the site for the purpose of protecting nearby persons, property, or the environment from the effects of the release. They are trained to respond in a defensive fashion without actually trying to stop the release. Their function is to contain the release from a safe distance, keep it from spreading, and prevent exposures. First responders at the operational level shall have received at least eight hours of training or have had sufficient experience to objectively demonstrate competency in the following areas in addition to those listed for the awareness level and the employer shall so certify:
(A) Knowledge of the basic hazard and risk assessment techniques.
(B) Know how to select and use proper personal protective equipment provided to the first responder operational level.
(C) An understanding of basic hazardous materials terms.
(D) Know how to perform basic control, containment and/or confinement operations within the capabilities of the resources and personal protective equipment available with their unit.
(E) Know how to implement basic decontamination procedures.
(F) An understanding of the relevant standard operating procedures and termination procedures.
(iii) – Hazardous materials technician. Hazardous materials technicians are individuals who respond to releases or potential releases for the purpose of stopping the release. They assume a more aggressive role than a first responder at the operations level in that they will approach the point of release in order to plug, patch or otherwise stop the release of a hazardous substance. Hazardous materials technicians shall have received at least 24 hours of training equal to the first responder operations level and in addition have competency in the following areas and the employer shall so certify:
(A) Know how to implement the employer’s emergency response plan.
(B) Know the classification, identification and verification of known and unknown materials by using field survey instruments and equipment.
(C) Be able to function within an assigned role in the Incident Command System.
(D) Know how to select and use proper specialized chemical personal protective equipment provided to the hazardous materials technician.
(E) Understand hazard and risk assessment techniques.
(F) Be able to perform advance control, containment, and/or confinement operations within the capabilities of the resources and personal protective equipment available with the unit.
(G) Understand and implement decontamination procedures.
(H) Understand termination procedures.
(I) Understand basic chemical and toxicological terminology and behavior.
(iv) – Hazardous materials specialist. Hazardous materials specialists are individuals who respond with and provide support to hazardous materials technicians. Their duties parallel those of the hazardous materials technician, however, those duties require a more directed or specific knowledge of the various substances they may be called upon to contain. The hazardous materials specialist would also act as the site liaison with Federal, state, local and other government authorities in regards to site activities. Hazardous materials specialists shall have received at least 24 hours of training equal to the technician level and in addition have competency in the following areas and the employer shall so certify:
(A) Know how to implement the local emergency response plan.
(B) Understand classification, identification and verification of known and unknown materials by using advanced survey instruments and equipment.
(C) Know the state emergency response plan.
(D) Be able to select and use proper specialized chemical personal protective equipment provided to the hazardous materials specialist.
(E) Understand in-depth hazard and risk techniques.
(F) Be able to perform specialized control, containment, and/or confinement operations within the capabilities of the resources and personal protective equipment available.
(G) Be able to determine and implement decontamination procedures.
(H) Have the ability to develop a site safety and control plan.
(I) Understand chemical, radiological and toxicological terminology and behavior.
(v) – On scene incident commander. Incident commanders, who will assume control of the incident scene beyond the first responder awareness level, shall receive at least 24 hours of training equal to the first responder operations level and in addition have competency in the following areas and the employer shall so certify:
(A) Know and be able to implement the employer’s incident command system.
(B) Know how to implement the employer’s emergency response plan.
(C) Know and understand the hazards and risks associated with employees working in chemical protective clothing.
(D) Know how to implement the local emergency response plan.
(E) Know of the state emergency response plan and of the Federal Regional Response Team.
(F) Know and understand the importance of decontamination procedures.
(q)(7) – Trainers. Trainers who teach any of the above training subjects shall have satisfactorily completed a training course for teaching the subjects they are expected to teach, such as the courses offered by the U.S. National Fire Academy, or they shall have the training and/or academic credentials and instructional experience necessary to demonstrate competent instructional skills and a good command of the subject matter of the courses they are to teach.
(q)(8)- Refresher training.
(i) Those employees who are trained in accordance with paragraph (q)(6) of this section shall receive annual refresher training of sufficient content and duration to maintain their competencies, or shall demonstrate competency in those areas at least yearly.
(ii) A statement shall be made of the training or competency, and if a statement of competency is made, the employer shall keep a record of the methodology used to demonstrate competency.
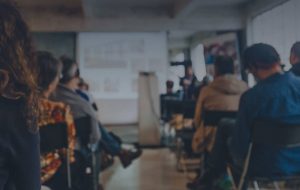
On Site Hazwoper Training Classes
OSHA authorized OSHA trainer comes to your site to conduct a Hazwoper training class for your group of 10 or more trainees.
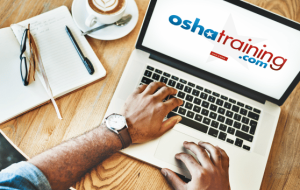
Online Hazwoper Training Courses
On demand OSHA training courses for all the most popular Hazwoper courses (24-hour, 40-hour, and 8-hour refresher).
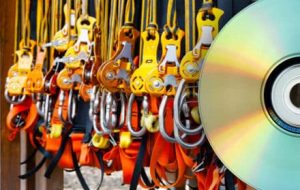