OSHA Administrative Training Requirements
Home More Training Resources OSHA Administrative Training Requirements
Many standards promulgated by the Occupational Safety and Health Administration (OSHA) explicitly require the employer to train (or instruct, or communicate, or inform . . .) employees in the safety and health aspects of their jobs. Other OSHA standards make it the employer’s responsibility to limit certain job assignments to employees who are “certified,” “competent,” or “qualified” – meaning that they have had special previous training, in or out of the workplace. Also, the term “designated” personnel means selected or assigned by the employer or the employer’s representative as being qualified to perform specific duties.
The OSHA training requirements listed below have been excerpted from Title 29, Code of Federal Regulations (CFR), Parts 1903 and 1904.
NOTICE – IMPORTANT INFORMATION:
- The OSHA training requirements listed on this website are only intended to provide users with a generic, non-exhaustive overview of the OSHA training requirements for specific standards-related topics. Most requirements for posting information, warning signs, labels, and the like are excluded from this information, as are most references to the qualifications of people assigned to test workplace conditions or equipment.
- This website is not the official or final authority to determine OSHA compliance responsibilities, which are set forth in OSHA standards themselves, and the Occupational Safety and Health Act of 1970. Because OSHA regulations are constantly being added, deleted, and/or revised, you must not rely on this website as the official or final authority of OSHA training requirements; refer to the official OSHA regulations available on OSHA’s website (osha.gov).
- Moreover, because interpretations and enforcement policy may change over time, the reader should consult administrative interpretations and decisions by the Occupational Safety and Health Review Commission and the courts. This information is also available on the OSHA website (osha.gov).
- Some states have implemented their own OSHA-approved state plan OSHA program with regulations affecting employee training that could differ from Federal OSHA’s, so consult your state regulations where applicable.
- In the absence of applicable training requirements for a particular work activity, hazardous substance, tool or piece of equipment or machinery, employers are encouraged to refer to manufacturers’ recommendations for safety training, where available, as well as those listed in applicable voluntary consensus standards.
- The information contained in this website is for informational purposes only, and should not be used to replace professional advice. Users of this website and their employers are responsible for how they choose to utilize this content, and OSHA Training Services Inc. assumes no liability for the use or misuse of the information contained herein.
1910.21 – 30 – Subpart D – Walking-Working Surfaces
1910.38 – Emergency Action Plans
1910.39 – Fire Prevention Plans
1910.66 – Powered Platforms for Building Maintenance
1910.95 – Occupational Noise Exposure
1910.106 – Flammable and Combustible Liquids
1910.109 – Explosive and Blasting Agents
1910.110 – Storage and Handling of Liquefied Petroleum Gases
1910.111 – Storage and Handling of Anhydrous Ammonia
1910.119 – Process Safety Management of Highly Hazardous Chemicals
1910.120 – Hazardous Waste Operations and Emergency Response
1910.124 – General Requirements for Dipping and Coating Operations
1910.132 – Personal Protective Equipment
1910.134 – Respiratory Protection
1910.142 – Temporary Labor Camps
1910.145 – Specifications for Accident Prevention Signs and Tags
1910.146 – Permit Required Confined Spaces
1910.147 – The Control of Hazardous Energy (lockout-tagout)
1910.151 – Medical Services and First-Aid
1910.155 – 1910.165 – Fire Protection (includes portable fire extinguishers)
1910.177 – Servicing of Multi-Piece and Single-Piece Rim Wheels
1910.178 – Powered Industrial Trucks (forklift operator training)
1910.179 – Overhead and Gantry Cranes
1910.180 – Crawler, Locomotives and Truck Cranes
1910.181 – Derricks (material handling)
1910.183 – Helicopters (for material handling)
1910.184 – Slings (material handling)
1910.217 – Mechanical Power Presses
1910.218 – Forging Machines
1910.252 – 1910.255 – Welding, Cutting and Brazing
1910.261 – Pulp, Paper, and Paperboard Mills
1910.262 – Textiles
1910.264 – Laundry Machinery and Operations
1910.265 – Sawmills
1910.266 – Logging Operations
1910.268 – Telecommunications
1910.269 – Electric Power Generation, Transmission, and Distribution
1910.272 – Grain Handling Facilities
1910.332 – 1910.333 – Electrical Safety Related Work Practices
1910.410 – 1910.440 – Commercial Diving Operations
1910.1000 – Toxic and Hazardous Substances
1910.1001 – Asbestos
1910.1003 – 1910.1016 – Thirteen Carcinogens
1910.1017 – Vinyl Chloride
1910.1018 – Inorganic Arsenic
1910.1020 – Access to Employee Exposure and Medical Records
1910.1025 – Lead
1910.1026 – Chromium (VI)
1910.1027 – Cadmium
1910.1028 – Benzene
1910.1029 – Coke Oven Emissions
1910.1030 – Bloodborne Pathogens
1910.1043 – Cotton Dust
1910.1044 – 1,2-Dibromo-3-Chloropropane
1910.1045 – Acrylonitrile (Vinyl Cyanide)
1910.1047 – Ethylene Oxide
1910.1048 – Formaldehyde
1910.1050 – Methylenedianiline
1910.1051 – 1,3-Butadiene
1910.1052 – Methylene Chloride
1910.1096 – Ionizing Radiation
1910.1200 – Hazard Communication
1910.1450 – Occupational Exposure to Hazardous Chemicals in Laboratories
1926.20 – General Safety and Health Provisions
1926.21 – Safety Training and Education
1926.33 – Access to Employee Exposure and Medical Records*
1926.35 – Employee Emergency Action Plans
1925.50 – Medical Services and First Aid
1926.53 – Ionizing Radiation
1926.54 – Non-ionizing Radiation
1926.55 – Gases, Vapors, Fumes, Dusts, and Mists
1926.59 – Hazard Communication*
1926.60 – Methylenedianiline
1926.62 – Lead
1926.64 – Process Safety Management
1926.65 – Hazardous Waste Operations and Emergency Response
1926.101 – Hearing Protection
1926.103 – Respiratory Protection*
1926.150 – Fire Protection
1926.201 – Signaling
1926.202 – Barricades
1926.302 – Powder-Operated Hand Tools
1926.304 – Woodworking Tools
1926.350 – 1926.354 – Welding and Cutting
1926.404 – Wiring Design and Protection
1926.451 – 1926.454 – Scaffolding
1926.500 – 1926.503 – Fall Protection
1926.551 – Helicopters
1926.552 – Material Hoists, Personnel Hoists, and Elevators
1926.602 – Material Handling Equipment
1926.604 – Site Clearing
1926.650 – 1926.652 – Excavations
1926.700 – 1926.706 – Concrete and Masonry Construction
1926.750 – 1926.761 – Steel Erection
1926.800 – 1926.804 – Underground Construction, Caissons, Cofferdams, and Compressed Air
1926.850 – 1926.860 – Demolition
1926.900 – 1926.914 – Blasting and the Use of Explosives
1926.950 – 1926.960 – Power Transmission and Distribution
1926.1050 – 1926.1060 – Ladders (and Stairways)
1926.1071 – 1926.1091 – Commercial Diving Operations*
1926.1101 – Asbestos
1926.1103 – 1926.1016 – Thirteen Carcinogens*
1926.1117 – Vinyl Chloride*
1926.1118 – Inorganic Arsenic*
1926.1126 – Chromium (VI)
1926.1127 – Cadmium
1926.1128 – Benzene*
1926.1129 – Coke Oven Emissions*
1926.1144 – 1,2-dibromo-3-chloropropane*
1926.1145 – Acrylonitrile*
1926.1147 – Ethylene Oxide*
1926.1148 – Formaldehyde*
1926.1152 – Methylene Chloride*
1926.1200 – 1926.1013 – Confined Spaces in Construction
1926.1400 – 1926.1442 – Cranes & Derricks in Construction
1926.1500 – 1926.1501 – Cranes and Derricks Used in Demolition and Underground Construction
* The OSHA Construction standards listed above that have been marked with an asterisk (*) are identical to those set forth in the General Industry standard with the same name in Part 1910.
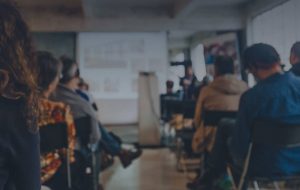
On Site OSHA Training Classes
OSHA authorized OSHA trainer comes to your site to conduct an OSHA training class for your group of 8 or more trainees.
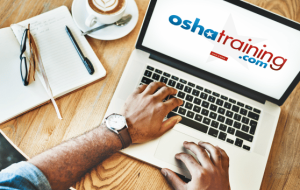
Online OSHA Training Courses
On demand OSHA training courses for all the most popular topics. OSHA 10 hour, OSHA 30 hour, confined space, Hazwoper, & more.
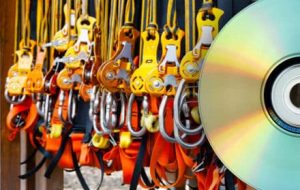
OSHA Training DVDs with Leader's Guide
Conduct in-house OSHA training classes yourself with our OSHA training DVD's. Each one comes with a leader's guide.