Welding and Cutting – 1926 Construction
Home More Training Resources OSHA Construction Industry Training Requirements Welding and Cutting – 1926 Construction
OSHA Construction Training Requirements - WELDING AND CUTTING
This website is not the official or final authority to determine OSHA compliance responsibilities, which are set forth in OSHA standards themselves, and the Occupational Safety and Health Act of 1970. Because OSHA regulations are constantly being added, deleted, and/or revised, you must not rely on this website as the official or final authority of OSHA training requirements; refer to the official OSHA regulations available on OSHA’s website (osha.gov). – See disclaimers.
1926.350 – 1926.354 – Welding and Cutting
1926.350 – Gas Welding and Cutting
(d) – Use of fuel gas. The employer shall thoroughly instruct employees in the safe use of fuel gas, as follows:
(1) – Before a regulator to a cylinder valve is connected, the valve shall be opened slightly and closed immediately. (This action is generally termed “cracking” and is intended to clear the valve of dust or dirt that might otherwise enter the regulator.) The person cracking the valve shall stand to one side of the outlet, not in front of it. The valve of a fuel gas cylinder shall not be cracked where the gas would reach welding work, sparks, flame, or other possible sources of ignition.
(2) – The cylinder valve shall always be opened slowly to prevent damage to the regulator. For quick closing, valves on fuel gas cylinders shall not be opened more than 1 1/2 turns. When a special wrench is required, it shall be left in position on the stem of the valve while the cylinder is in use so that the fuel gas flow can be shut off quickly in case of an emergency. In the case of manifolded or coupled cylinders, at least one such wrench shall always be available for immediate use. Nothing shall be placed on top of a fuel gas cylinder, when in use, which may damage the safety device or interfere with the quick closing of the valve.
(3) – Fuel gas shall not be used from cylinders through torches or other devices which are equipped with shutoff valves without reducing the pressure through a suitable regulator attached to the cylinder valve or manifold.
(4) – Before a regulator is removed from a cylinder valve, the cylinder valve shall always be closed and the gas released from the regulator.
(5) – If, when the valve on a fuel gas cylinder is opened, there is found to be a leak around the valve stem, the valve shall be closed and the gland nut tightened. If this action does not stop the leak, the use of the cylinder shall be discontinued, and it shall be properly tagged and removed from the work area. In the event that fuel gas should leak from the cylinder valve, rather than from the valve stem, and the gas cannot be shut off, the cylinder shall be properly tagged and removed from the work area. If a regulator attached to a cylinder valve will effectively stop a leak through the valve seat, the cylinder need not be removed from the work area.
(6) – If a leak should develop at a fuse plug or other safety device, the cylinder shall be removed from the work area.
(j) – Additional rules. For additional details not covered in this subpart, applicable technical portions of American National Standards Institute, Z49.1-1967, Safety in Welding and Cutting, shall apply.
From ANSI Standard Z49.1-1967, Fire Watch Duties: “Fire watchers shall be trained in the use of fire extinguishing equipment. They shall be familiar with facilities for sounding an alarm in the event of a fire. They shall watch for fires in all exposed areas, try to extinguish them only when obviously within the capacity of the equipment available, or otherwise sound the alarm. A fire watch shall be maintained for at least a half hour after completion of welding or cutting operations to detect and extinguish possible smoldering fires.”
1926.351 – Arc Welding and Cutting
(d) – Operating instructions. Employers shall instruct employees in the safe means of arc welding and cutting as follows:
(1) – When electrode holders are to be left unattended, the electrodes shall be removed and the holders shall be so placed or protected that they cannot make electrical contact with employees or conducting objects.
(2) – Hot electrode holders shall not be dipped in water; to do so may expose the arc welder or cutter to electric shock.
(3) – When the arc welder or cutter has occasion to leave his work or to stop work for any appreciable length of time, or when the arc welding or cutting machine is to be moved, the power supply switch to the equipment shall be opened.
(4) – Any faulty or defective equipment shall be reported to the supervisor.
1926.352 – Fire Prevention
(e) – When the welding, cutting, or heating operation is such that normal fire prevention precautions are not sufficient, additional personnel shall be assigned to guard against fire while the actual welding, cutting, or heating operation is being performed, and for a sufficient period of time after completion of the work to ensure that no possibility of fire exists. Such personnel shall be instructed as to the specific anticipated fire hazards and how the firefighting equipment provided is to be used.
1926.353 – Ventilation and protection in welding, cutting, and heating
(b) – Welding, cutting, and heating in confined spaces.
(2) – When sufficient ventilation cannot be obtained without blocking the means of access, employees in the confined space shall be protected by air-line respirators in accordance with the requirements of Subpart E of this part, and an employee on the outside of such a confined space shall be assigned to maintain communication with those working within it and to aid them in an emergency.
(3) – “Lifelines.” Where a welder must enter a confined space through a manhole or other small opening, means shall be provided for quickly removing him in case of emergency. When safety belts and lifelines are used for this purpose they shall be so attached to the welder’s body that his body cannot be jammed in a small exit opening. An attendant with a pre-planned rescue procedure shall be stationed outside to observe the welder at all times and be capable of putting rescue operations into effect.
(c) – Welding, cutting, or heating of metals of toxic significance.
(2) – Welding, cutting, or heating in any enclosed spaces involving the metals specified in this subparagraph shall be performed with local exhaust ventilation in accordance with the requirements of paragraph (a) of this section, or employees shall be protected by air-line respirators in accordance with the requirements of Subpart E of this part:
(3) – Employees performing such operations in the open air shall be protected by filter-type respirators in accordance with the requirements of Subpart E of this part, except that employees performing such operations on beryllium-containing base or filler metals shall be protected by air-line respirators in accordance with the requirements of Subpart E of this part.
1926.354 – Welding, Cutting, and Heating in Way of Preservative Coatings
(a) – Before welding, cutting, or heating is commenced on any surface covered by a preservative coating whose flammability is not known, a test shall be made by a competent person to determine its flammability. Preservative coatings shall be considered to be highly flammable when scrapings burn with extreme rapidity.
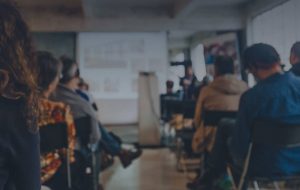
On Site OSHA Training Classes
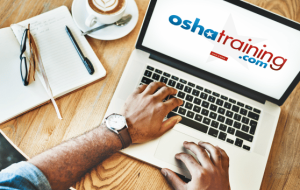
Online OSHA Training Courses
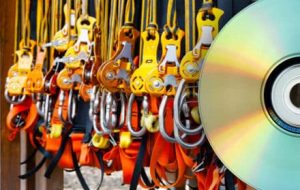