Read our OSHA training Blog Posts Written by an OSHA Expert
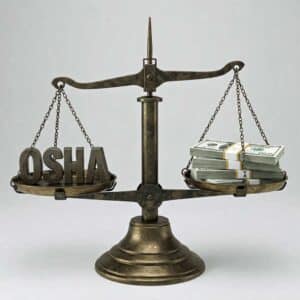
Debunking the Myth: OSHA is NOT Self-Funded
Is OSHA a Self-Funded Agency? I was chatting with a fellow safety professional the other day, someone I consider a very seasoned pro, to discuss
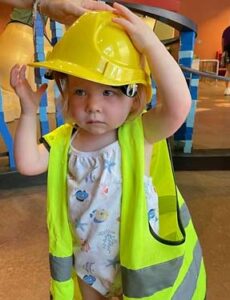
Does OSHA Have an Age Restriction for OSHA 10 Training?
OSHA 10-hour Training for Younger Workers Occupational Safety and Health Administration (OSHA) 10-hour training plays a crucial role in enhancing workplace safety across various industries
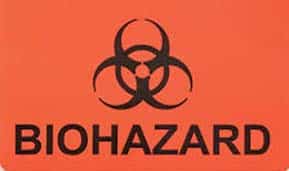
Do Your Employees Have “Occupational Exposure” to Bloodborne Pathogens?
It happens more times than I care to admit. I am discussing the topic of OSHA’s Bloodborne Pathogens (BBP) standard with a client or students
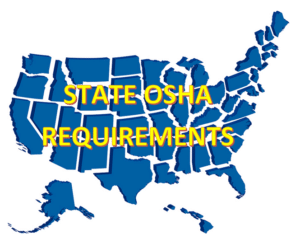
Unique, Interesting, and Quirky State OSHA Standards
Don’t Let These State OSHA Requirements Catch You By Surprise Over half of the states and territories administer an approved State Plan OSHA Program, which
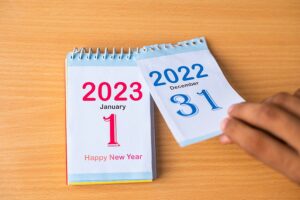
OSHA’s Mandatory Annual Refresher Training Requirements
OSHA Training Required Year After Year . . . The new year is in full swing now, so it’s time to start planning your OSHA
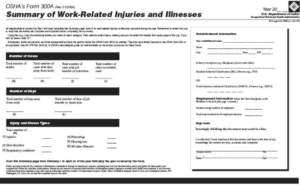
Common Mistakes on OSHA Injury & Illness Recordkeeping Forms
Avoid These OSHA Recordkeeping Errors Here, in no particular order, is my personal list of the ten most common mistakes found on OSHA Injury and
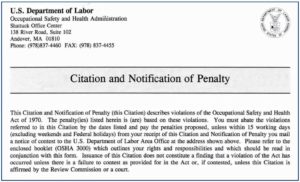
How To Fight OSHA Citations and Monetary Penalties
OSHA Expert Explains Options to Handle OSHA Citations and Penalties When OSHA believes that an employer is in violation of one or more of their
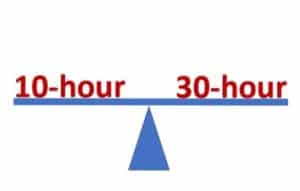
Considerations When Selecting OSHA 10-hour or OSHA 30-hour Training Courses
Do You Need OSHA 10-hour Training, 30-hour Training, or Both? Employers and employees looking to get educated on OSHA standards and workplace hazards often turn
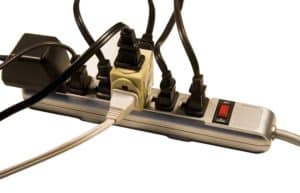
Misuse of Power Strips, Surge Protectors, and Receptacle Boxes
OSHA Requirements for UL Rated Electrical Equipment Power Strips; You’ll often find them in offices with printers, computers plugged into them, or in some cases
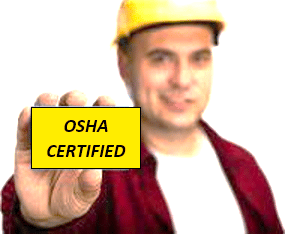
The Truth About “OSHA Certification”
If I’ve heard it once, I’ve heard it a thousand times! An employer will call and say “My supervisors all need their OSHA 30 certification”.
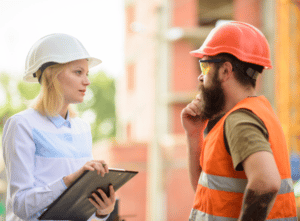
I Made OSHA Get a Warrant to Conduct an Inspection; Here’s What Happened.
Imagine if a police officer came to your home, knocked on your door, and said he just happens to be in your neighborhood and wanted
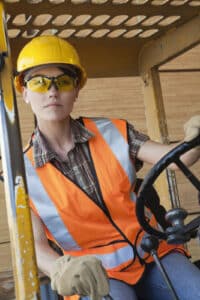
OSHA Forklift / Powered Industrial Truck Operator Training – Myths Busted
I’ve conducted numerous audits of company’s safety training records throughout the years, and have picked up on some common mistakes that are repeated by many
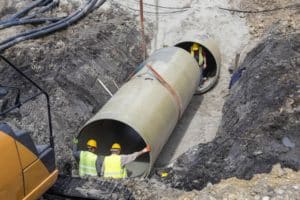
Are Trenches & Other Excavations Permit-required Confined Spaces?
I’ve taught a lot of excavation competent person training classes over the years, and more times than not I get the following question: “Trenches and
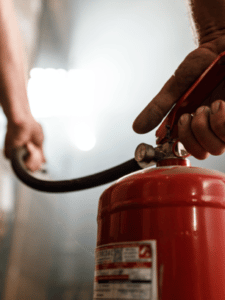
Fire Extinguishers: Is Hands-on Training Required?
One question I get asked a lot is whether or not the Federal OSHA standards for portable fire extinguishers requires employees to perform “hands on”
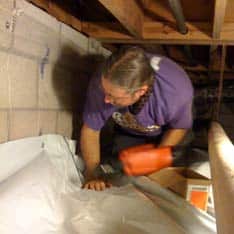
Misunderstandings About OSHA’s Confined Spaces Standard
Differences from general industry Confined Space Standards Spur Confusion When OSHA published their Permit-required Confined Space standard (1910.146), it was inevitable that some people would
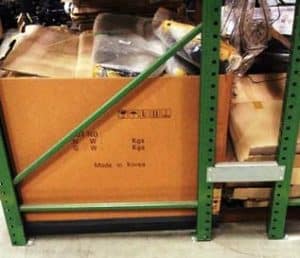
OSHA Requirements to Secure Pallet Racks
Are There OSHA Standards for Securing Pallet Racks? One follower of our OSHA training blog submitted this commonly-asked question to be discussed . . .
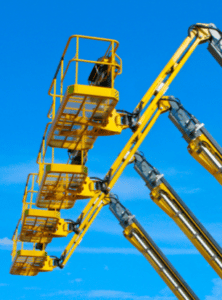
Fall Protection Requirements for Aerial Lifts
When I first set down and began drafting this blog post, I started off with the intent to address the many different fall protection requirements
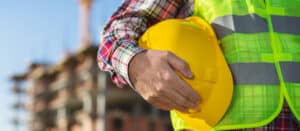
Answers to Top Five Questions about Hard Hats
Over the years I’ve noticed there are five questions about hard hats that are repeatedly asked. However, the Federal OSHA standards on head protection do
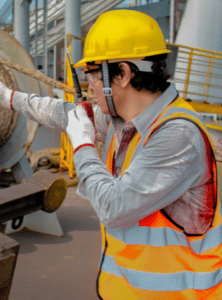
OSHA Regulations on Cell Phone Use at Work
Is it Smart to Use Your Cell Phone While At Work? I got my first cell phone way back in the 1980’s, when they were