Hazard Communication
Home More Training Resources OSHA General Industry Training Requirements Hazard Communication
OSHA Training Requirements - Hazard Communication
This website is not the official or final authority to determine OSHA compliance responsibilities, which are set forth in OSHA standards themselves, and the Occupational Safety and Health Act of 1970. Because OSHA regulations are constantly being added, deleted, and/or revised, you must not rely on this website as the official or final authority of OSHA training requirements; refer to the official OSHA regulations available on OSHA’s website (osha.gov). – See disclaimers.
1910.1200 – Hazard Communication
(a) – Purpose.
(1) – The purpose of this section is to ensure that the hazards of all chemicals produced or imported are classified, and that information concerning the classified hazards is transmitted to employers and employees. The requirements of this section are intended to be consistent with the provisions of the United Nations Globally Harmonized System of Classification and Labelling of Chemicals (GHS), Revision 3. The transmittal of information is to be accomplished by means of comprehensive hazard communication programs, which are to include container labeling and other forms of warning, safety data sheets and employee training.
(2) – This occupational safety and health standard is intended to address comprehensively the issue of classifying the potential hazards of chemicals, and communicating information concerning hazards and appropriate protective measures to employees, and to preempt any legislative or regulatory enactments of a state, or political subdivision of a state, pertaining to this subject. Classifying the potential hazards of chemicals and communicating information concerning hazards and appropriate protective measures to employees, may include, for example, but is not limited to, provisions for: developing and maintaining a written hazard communication program for the workplace, including lists of hazardous chemicals present; labeling of containers of chemicals in the workplace, as well as of containers of chemicals being shipped to other workplaces; preparation and distribution of safety data sheets to employees and downstream employers; and development and implementation of employee training programs regarding hazards of chemicals and protective measures. Under section 18 of the Act, no state or political subdivision of a state may adopt or enforce any requirement relating to the issue addressed by this Federal standard, except pursuant to a Federally-approved state plan.
(b) – Scope and application.
(1) – This section requires chemical manufacturers or importers to classify the hazards of chemicals which they produce or import, and all employers to provide information to their employees about the hazardous chemicals to which they are exposed, by means of a hazard communication program, labels and other forms of warning, safety data sheets, and information and training. In addition, this section requires distributors to transmit the required information to employers. (Employers who do not produce or import chemicals need only focus on those parts of this rule that deal with establishing a workplace program and communicating information to their workers.)
(iii) Employers shall ensure that laboratory employees are provided information and training in accordance with paragraph (h) of this section, except for the location and availability of the written hazard communication program under paragraph (h)(2)(iii) of this section; and,
(4) – In work operations where employees only handle chemicals in sealed containers which are not opened under normal conditions of use (such as are found in marine cargo handling, warehousing, or retail sales), this section applies to these operations only as follows:
(iii) Employers shall ensure that employees are provided with information and training in accordance with paragraph (h) of this section (except for the location and availability of the written hazard communication program under paragraph (h)(2)(iii) of this section), to the extent necessary to protect them in the event of a spill or leak of a hazardous chemical from a sealed container.
(c) – Definitions.
Employee means a worker who may be exposed to hazardous chemicals under normal operating conditions or in foreseeable emergencies. Workers such as office workers or bank tellers who encounter hazardous chemicals only in non-routine, isolated instances are not covered.
(e) – Written hazard communication program.
(1) – Employers shall develop, implement, and maintain at each workplace, a written hazard communication program which at least describes how the criteria specified in paragraphs (f), (g), and (h) of this section for labels and other forms of warning, safety data sheets, and employee information and training will be met, and which also includes the following:
(ii) The methods the employer will use to inform employees of the hazards of non-routine tasks (for example, the cleaning of reactor vessels), and the hazards associated with chemicals contained in unlabeled pipes in their work areas.’
(2) – Multi-employer workplaces. Employers who produce, use, or store hazardous chemicals at a workplace in such a way that the employees of other employer(s) may be exposed (for example, employees of a construction contractor working on-site) shall additionally ensure that the hazard communication programs developed and implemented under this paragraph (e) include the following:
(ii) The methods the employer will use to inform the other employer(s) of any precautionary measures that need to be taken to protect employees during the workplace’s normal operating conditions and in foreseeable emergencies; and,
(iii) The methods the employer will use to inform the other employer(s) of the labeling system used in the workplace.
(f) – Labels and other forms of warning.
(10) – The employer shall ensure that workplace labels or other forms of warning are legible, in English, and prominently displayed on the container, or readily available in the work area throughout each work shift. Employers having employees who speak other languages may add the information in their language to the material presented, as long as the information is presented in English as well.
(h) – Employee information and training.
(1) – Employers shall provide employees with effective information and training on hazardous chemicals in their work area at the time of their initial assignment, and whenever a new chemical hazard the employees have not previously been trained about is introduced into their work area. Information and training may be designed to cover categories of hazards (e.g., flammability, carcinogenicity) or specific chemicals. Chemical-specific information must always be available through labels and safety data sheets.
(2) – Information. Employees shall be informed of:
(i) The requirements of this section;
(ii) Any operations in their work area where hazardous chemicals are present; and,
(iii) The location and availability of the written hazard communication program, including the required list(s) of hazardous chemicals, and safety data sheets required by this section.
(3) – Training. Employee training shall include at least:
(i) Methods and observations that may be used to detect the presence or release of a hazardous chemical in the work area (such as monitoring conducted by the employer, continuous monitoring devices, visual appearance or odor of hazardous chemicals when being released, etc.);
(ii) The physical, health, simple asphyxiation, combustible dust, and pyrophoric gas hazards, as well as hazards not otherwise classified, of the chemicals in the work area;
(iii) The measures employees can take to protect themselves from these hazards, including specific procedures the employer has implemented to protect employees from exposure to hazardous chemicals, such as appropriate work practices, emergency procedures, and personal protective equipment to be used; and,
(iv) The details of the hazard communication program developed by the employer, including an explanation of the labels received on shipped containers and the workplace labeling system used by their employer; the safety data sheet, including the order of information and how employees can obtain and use the appropriate hazard information.
(j) – Effective dates.
(1) – Employers shall train employees regarding the new label elements and safety data sheets format by December 1, 2013.
Note: The text above has been updated to reflect the requirements of OSHA’s revised Hazard Communication Standard. That standard was revised to align with the United Nation’s Globally Harmonized System of Classification and Labeling of Chemicals (GHS), Revision 3, published in the Federal Register on March 26, 2012. This revised OSHA Haz-Com standard became effective on May 25, 2012.
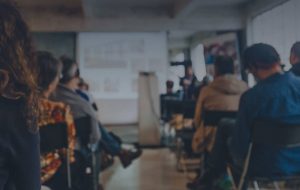
On Site OSHA Training Classes
OSHA authorized OSHA trainer comes to your site to conduct an OSHA training class for your group of 10 or more trainees.
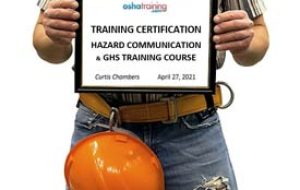
Online Hazard Communication Training Courses
On demand OSHA training courses for Hazard Communication / GHS compliance. Initial training and refresher training courses.
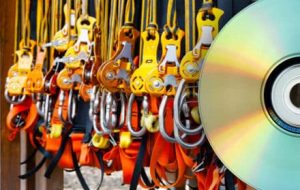
Haz-Com Training DVD with Leader's Guide
Conduct OSHA training in-house with our Hazard Communication / GHS training DVD with leader guide.