Electric Power Generation, Transmission, and Distribution
Home More Training Resources OSHA General Industry Training Requirements Electric Power Generation, Transmission, and Distribution
OSHA Training Requirements - Electric Power Generation, Transmission and Distribution
This website is not the official or final authority to determine OSHA compliance responsibilities, which are set forth in OSHA standards themselves, and the Occupational Safety and Health Act of 1970. Because OSHA regulations are constantly being added, deleted, and/or revised, you must not rely on this website as the official or final authority of OSHA training requirements; refer to the official OSHA regulations available on OSHA’s website (osha.gov). – See disclaimers.
1910.269 – Electric Power Generation, Transmission, and Distribution
(a)(2) – “Training.”
(i) Employees shall be trained in and familiar with the safety-related work practices, safety procedures, and other safety requirements in this section that pertain to their respective job assignments. Employees shall also be trained in and familiar with any other safety practices, including applicable emergency procedures (such as pole top and manhole rescue), that are not specifically addressed by this section but that are related to their work and are necessary for their safety.
(ii) Qualified employees shall also be trained and competent in:
(A) – The skills and techniques necessary to distinguish exposed live parts from other parts of electric equipment,
(B) – The skills and techniques necessary to determine the nominal voltage of exposed live parts,
(C) – The minimum approach distances specified in this section corresponding to the voltages to which the qualified employee will be exposed, and
(D) – The proper use of the special precautionary techniques, personal protective equipment, insulating and shielding materials, and insulated tools for working on or near exposed energized parts of electric equipment.
Note: For the purposes of this section, a person must have this training in order to be considered a qualified person.
(iii) The employer shall determine, through regular supervision and through inspections conducted on at least an annual basis, that each employee is complying with the safety-related work practices required by this section.
(iv) An employee shall receive additional training (or retraining) under any of the following conditions:
(A) – If the supervision and annual inspections required by paragraph (a)(2)(iii) of this section indicate that the employee is not complying with the safety-related work practices required by this section, or
(B) – If new technology, new types of equipment, or changes in procedures necessitate the use of safety-related work practices that are different from those which the employee would normally use, or
(C) – If he or she must employ safety-related work practices that are not normally used during his or her regular job duties.
Note: OSHA would consider tasks that are performed less often than once per year to necessitate retraining before the performance of the work practices involved.
(v) The training required by paragraph (a)(2) of this section shall be of the classroom or on-the-job type.
(vi) The training shall establish employee proficiency in the work practices required by this section and shall introduce the procedures necessary for compliance with this section.
(vii) The employer shall certify that each employee has received the training required by paragraph (a)(2) of this section. This certification shall be made when the employee demonstrates proficiency in the work practices involved and shall be maintained for the duration of the employee’s employment.
Note: Employment records that indicate that an employee has received the required training are an acceptable means of meeting this requirement.
(b) – “Medical services and first aid.” The employer shall provide medical services and first aid as required in 1910.151 of this Part. In addition to the requirements of 1910.151 of this Part, the following requirements also apply:
(1) – “Cardiopulmonary resuscitation and first aid training.” When employees are performing work on or associated with exposed lines or equipment energized at 50 volts or more, persons trained in first aid including cardiopulmonary resuscitation (CPR) shall be available as follows:
(i) For field work involving two or more employees at a work location, at least two trained persons shall be available. However, only one trained person need be available if all new employees are trained in first aid, including CPR, within 3 months of their hiring dates.
(ii) For fixed work locations such as generating stations, the number of trained persons available shall be sufficient to ensure that each employee exposed to electric shock can be reached within 4 minutes by a trained person. However, where the existing number of employees is insufficient to meet this requirement (at a remote substation, for example), all employees at the work location shall be trained.
(c) – “Job briefing.” The employer shall ensure that the employee in charge conducts a job briefing with the employees involved before they start each job. The briefing shall cover at least the following subjects: hazards associated with the job, work procedures involved, special precautions, energy source controls, and personal protective equipment requirements.
(1) – “Number of briefings.” If the work or operations to be performed during the work day or shift are repetitive and similar, at least one job briefing shall be conducted before the start of the first job of each day or shift. Additional job briefings shall be held if significant changes, which might affect the safety of the employees, occur during the course of the work.
(2) – “Extent of briefing.” A brief discussion is satisfactory if the work involved is routine and if the employee, by virtue of training and experience, can reasonably be expected to recognize and avoid the hazards involved in the job. A more extensive discussion shall be conducted:
(i) If the work is complicated or particularly hazardous, or
(ii) If the employee cannot be expected to recognize and avoid the hazards involved in the job.
Note: The briefing is always required to touch on all the subjects listed in the introductory text to paragraph (c) of this section.
(d)(2)(i) – The employer shall establish a program consisting of energy control procedures, employee training, and periodic inspections to ensure that, before any employee performs any servicing or maintenance on a machine or equipment where the unexpected energizing, start up, or release of stored energy could occur and cause injury, the machine or equipment is isolated from the energy source and rendered inoperative.
(d)(2)(v)(C) – If lockout is used for energy control, the periodic inspection shall include a review, between the inspector and each authorized employee, of that employee’s responsibilities under the energy control procedure being inspected.
(d)(2)(v)(D) – Where tagout is used for energy control, the periodic inspection shall include a review, between the inspector and each authorized and affected employee, of that employee’s responsibilities under the energy control procedure being inspected, and the elements set forth in paragraph (d)(2)(vii) of this section.
(d)(2)(vi) – The employer shall provide training to ensure that the purpose and function of the energy control program are understood by employees and that the knowledge and skills required for the safe application, usage, and removal of energy controls are acquired by employees. The training shall include the following:
(A) – Each authorized employee shall receive training in the recognition of applicable hazardous energy sources, the type and magnitude of energy available in the workplace, and in the methods and means necessary for energy isolation and control.
(B) – Each affected employee shall be instructed in the purpose and use of the energy control procedure.
(C) – All other employees whose work operations are or may be in an area where energy control procedures may be used shall be instructed about the procedures and about the prohibition relating to attempts to restart or reenergize machines or equipment that are locked out or tagged out.
(d)(2)(vii) – When tagout systems are used, employees shall also be trained in the following limitations of tags:
(A) – Tags are essentially warning devices affixed to energy isolating devices and do not provide the physical restraint on those devices that is provided by a lock.
(B) – When a tag is attached to an energy isolating means, it is not to be removed without authorization of the authorized person responsible for it, and it is never to be bypassed, ignored, or otherwise defeated.
(C) – Tags must be legible and understandable by all authorized employees, affected employees, and all other employees whose work operations are or may be in the area, in order to be effective.
(D) – Tags and their means of attachment must be made of materials which will withstand the environmental conditions encountered in the workplace.
(E) – Tags may evoke a false sense of security, and their meaning needs to be understood as part of the overall energy control program.
(F) – Tags must be securely attached to energy isolating devices so that they cannot be inadvertently or accidentally detached during use.
(d)(2)(viii) – Retraining shall be provided by the employer as follows:
(A) – Retraining shall be provided for all authorized and affected employees whenever there is a change in their job assignments, a change in machines, equipment, or processes that present a new hazard or whenever there is a change in the energy control procedures.
(B) – Retraining shall also be conducted whenever a periodic inspection under paragraph (d)(2)(v) of this section reveals, or whenever the employer has reason to believe, that there are deviations from or inadequacies in an employee’s knowledge or use of the energy control procedures.
(C) – The retraining shall reestablish employee proficiency and shall introduce new or revised control methods and procedures, as necessary.
(d)(2)(ix) – The employer shall certify that employee training has been accomplished and is being kept up to date. The certification shall contain each employee’s name and dates of training.
(d)(8)(iv) – Whenever outside servicing personnel are to be engaged in activities covered by paragraph (d) of this section, the on-site employer and the outside employer shall inform each other of their respective lockout or tagout procedures, and each employer shall ensure that his or her personnel understand and comply with restrictions and prohibitions of the energy control procedures being used.
(e)(2) – “Training.” Employees who enter enclosed spaces or who serve as attendants shall be trained in the hazards of enclosed space entry, in enclosed space entry procedures, and in enclosed space rescue procedures.
(e)(7) – “Attendants.” While work is being performed in the enclosed space, a person with first aid training meeting paragraph (b) of this section shall be immediately available outside the enclosed space to render emergency assistance if there is reason to believe that a hazard may exist in the space or if a hazard exists because of traffic patterns in the area of the opening used for entry. That person is not precluded from performing other duties outside the enclosed space if these duties do not distract the attendant from monitoring employees within the space. Note: See paragraph (t)(3) of this section for additional requirements on attendants for work in manholes.
(g)(2)(v) – Fall arrest equipment, work positioning equipment, or travel restricting equipment shall be used by employees working at elevated locations more than 4 feet (1.2 m) above the ground on poles, towers, or similar structures if other fall protection has not been provided. Fall protection equipment is not required to be used by a qualified employee climbing or changing location on poles, towers, or similar structures, unless conditions, such as, but not limited to, ice, high winds, the design of the structure (for example, no provision for holding on with hands), or the presence of contaminants on the structure, could cause the employee to lose his or her grip or footing.
Note 1: This paragraph applies to structures that support overhead electric power generation, transmission, and distribution lines and equipment. It does not apply to portions of buildings, such as loading docks, to electric equipment, such as transformers and capacitors, nor to aerial lifts. Requirements for fall protection associated with walking and working surfaces are contained in Subpart D of this Part; requirements for fall protection associated with aerial lifts are contained in 1910.67 of this Part.
Note 2: Employees undergoing training are not considered “qualified employees” for the purposes of this provision. Unqualified employees (including trainees) are required to use fall protection any time they are more than 4 feet (1.2 m) above the ground.
(l)(1) – “General.” Only qualified employees may work on or with exposed energized lines or parts of equipment. Only qualified employees may work in areas containing unguarded, uninsulated energized lines or parts of equipment operating at 50 volts or more. Electric lines and equipment shall be considered and treated as energized unless the provisions of paragraph (d) or paragraph (m) of this section have been followed.
(l)(6)(ii) – The employer shall train each employee who is exposed to the hazards of flames or electric arcs in the hazards involved.
(o)(2)(i) – The employer shall establish and enforce work practices for the protection of each worker from the hazards of high-voltage or high-power testing at all test areas, temporary and permanent. Such work practices shall include, as a minimum, test area guarding, grounding, and the safe use of measuring and control circuits. A means providing for periodic safety checks of field test areas shall also be included. (See paragraph (o)(6) of this section.)
(o)(2)(ii) – Employees shall be trained in safe work practices upon their initial assignment to the test area, with periodic reviews and updates provided as required by paragraph (a)(2) of this section.
(o)(4)(i) – The employer shall establish and implement safe grounding practices for the test facility.
(q)(3)(i) – Before using or supervising the use of the live-line bare-hand technique on energized circuits, employees shall be trained in the technique and in the safety requirements of paragraph (q)(3) of this section. Employees shall receive refresher training as required by paragraph (a)(2) of this section.
(t)(3)(i) – While work is being performed in a manhole containing energized electric equipment, an employee with first aid and CPR training meeting paragraph (b)(1) of this section shall be available on the surface in the immediate vicinity to render emergency assistance.
(u)(6)(i) – Upon entering an attended substation, each employee other than those regularly working in the station shall report his or her presence to the employee in charge in order to receive information on special system conditions affecting employee safety.
(u)(6)(ii) – The job briefing required by paragraph (c) of this section shall cover such additional subjects as the location of energized equipment in or adjacent to the work area and the limits of any deenergized work area.
(v)(11)(vii) – The employer shall ensure that employees who work in coal- or ash-handling conveyor areas are trained and knowledgeable in conveyor operation and in the requirements of paragraphs (v)(11)(viii) through (v)(11)(xii) of this section.
“Line-clearance tree trimmer – Definition. – ” An employee who, through related training or on-the-job experience or both, is familiar with the special techniques and hazards involved in line-clearance tree trimming.
Note 1: An employee who is regularly assigned to a line-clearance tree-trimming crew and who is undergoing on-the-job training and who, in the course of such training, has demonstrated an ability to perform duties safely at his or her level of training and who is under the direct supervision of a line-clearance tree trimmer is considered to be a line-clearance tree trimmer for the performance of those duties.
Note 2: A line-clearance tree trimmer is not considered to be a “qualified employee” under this section unless he or she has the training required for a qualified employee under paragraph (a)(2)(ii) of this section. However, under the electrical safety-related work practices standard in Subpart S of this Part, a line-clearance tree trimmer is considered to be a “qualified employee”. Tree trimming performed by such “qualified employees” is not subject to the electrical safety-related work practice requirements contained in 1910.331 through 1910.335 of this Part. (See also the note following 1910.332(b)(3) of this Part for information regarding the training an employee must have to be considered a qualified employee under 1910.331 through 1910.335 of this part.)
“Qualified employee” (qualified person) – Definition. – ” One knowledgeable in the construction and operation of the electric power generation, transmission, and distribution equipment involved, along with the associated hazards.
Note 1: An employee must have the training required by paragraph (a)(2)(ii) of this section in order to be considered a qualified employee.
Note 2: Except under paragraph (g)(2)(v) of this section, an employee who is undergoing on-the-job training and who, in the course of such training, has demonstrated an ability to perform duties safely at his or her level of training and who is under the direct supervision of a qualified person is considered to be a qualified person for the performance of those duties.
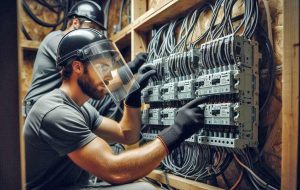
On Site NFPA 70E Training Classes
Trainer comes to your site to conduct NFPA 70E training for your group of 8 or more employees
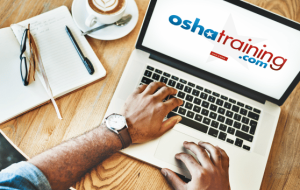
Online OSHA Training Courses
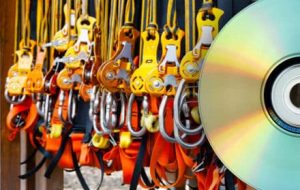